Scanning DPM Codes in the Automotive Industry
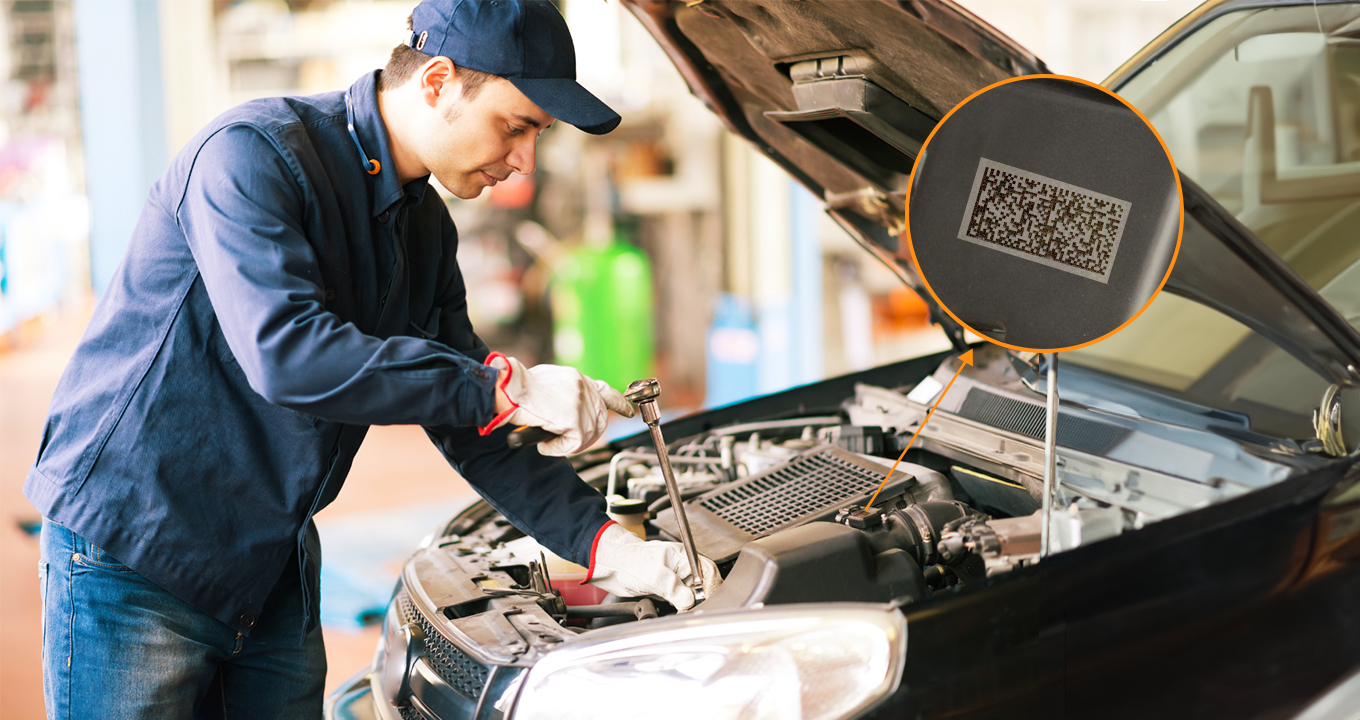
The automotive industry has fully adopted Direct Part Marking (DPM) codes, which facilitate the identification and monitoring of components during manufacturing. This blog examines the importance of DPM codes and investigates the difficulties encountered by conventional code scanning techniques within the automotive industry.
- The Rise of Scanning Technologies in the Automotive Industry
- Implementing DPM Code Scanning in Your Automotive Facility
- Getting Started with Dynamsoft Barcode Reader SDK
Understanding DPM Codes in Automotive Manufacturing
Accurate data capture is a fundamental aspect of quality control to achieve automotive manufacturing excellence. DPM codes serve as reliable indicators that aid in the rigorous monitoring and authentication of components utilized throughout the assembly line. In this section, we delve into the essential role of DPM codes in ensuring accuracy and efficiency throughout the manufacturing process.
Different Types of Automotive DPM Codes
Both DataMatrix codes and QR codes are used for Direct Part Marking. However, in the automotive industry, the DataMatrix format is most common.
It is widely used because it can store a lot of information in a small space (e.g. 2mm*2mm) due to high data density, remains durable with a matrix structure (readable even with partial damage), encodes different data types, and includes error correction for increased resistance to damage.
Types of Marking Specific to the Automotive Industry
DPM codes are available in various formats, each using unique marking technologies. This section provides a comprehensive analysis of the different DPM codes used within the automotive industry.
Laser Marking
Using a focused laser beam, laser marking produces distinct, high-contrast marks on different materials. A permanent mark is created when a minute quantity of material is eliminated or the laser beam triggers a chemical reaction.
Advantages of Laser Marking:
- Accuracy and resolution are high, making it ideal for complex patterns and tiny components.
- Useful for a lot of different materials, from metals to plastics.
- A non-contact approach that reduces equipment wear and tear.
Usage of Laser Marking
Due to its accuracy and durability, laser marking is widely used for serialization, part identification, and traceability.
CO2 Marking
CO2 marking uses a carbon dioxide laser to imprint designs onto a material’s surface through evaporation or discoloration. It is frequently applied to organic materials such as wood, paper and certain plastics.
Advantages of CO2 Marking
- Marks easily on a wide variety of surfaces.
- Cost-efficient for specific applications.
- Capable of marking at a rapid rate.
Usage of CO2 marking
In automotive, CO2 marking is mostly used for plastic components and labels.
Fiber Laser Marking
In fiber laser marking, laser beams are transmitted via fiber optic cable. It is ideal for marking plastics, metals and ceramics by producing of surface changes or color contrasts.
Advantages of Fiber Laser Marking:
- Fast, accurate marking.
- Appropriate for high-volume production.
- Long-lasting and requires no maintenance, as no moving parts are involved.
Usage of Fiber Laser
Metal items like engine components and chassis are frequently marked with fiber lasers for serialization and identification.
Chemical Etching
Chemical etching selectively eliminates material while marking the surface permanently, through chemical reaction.
Advantages of Chemical Etching:
- High accuracy and attention to detail
- Ideal for small as well as large production runs
- Suitable for labeling on non-uniform surfaces
Usage of Chemical Etching
Chemical etching is generally used to imprint identification information, logos, and serial numbers onto metal and alloy automotive components.
Dot Peen Marking
Dot peen marking is the process of indenting very small, closely spaced dots onto the surface of a material using a stylus, while exerting minimal force.
Advantages of Dot Peen Marking:
- Suitable for marking rigid substances, including metals.
- Environmentally resistant and long-lasting.
- Ideal for heavy and sizable components.
Usage of Dot Peen Marking
Due to its longevity, dot peen marking is frequently used to mark engine components and vehicle chassis directly.
Inkjet Marking
To mark a surface using an inkjet printer, ink is sprayed onto the target area at high pressure. As a contactless technique, it works well with many materials.
Advantages of Inkjet Marking:
- Ideal for printing on non-regular surfaces
- Fast marking capabilities
- Value for money for specific applications
Usage of Inkjet Marking
Inkjet marking is mainly used for labeling plastic components and automotive packaging.
Importance of Accurate Data Capture for Quality Control
DPM codes contain vital information for quality control. By generating a digital signature, a permanent and unique identifier is assigned to each component, enabling manufacturers to trace and verify components at every assembly line stage. Traceability is critical in checking appropriate placement of components and ensuring compliance with rigorous quality standards and regulatory requirements.
Limitations of Traditional Barcode Scanning in Automotive Manufacturing
Traditional barcode recognition faces considerable challenges within the rigorous environment of automotive manufacturing. Complexities arise due to problems scanning barcodes on reflective or irregular surfaces, which increases the likelihood of data capture errors.
Automobile components often have uneven surfaces, which presents difficulties for conventional scanners and may result in inaccuracies or potential production process disruptions. Reflective surfaces also impede the scanner’s capacity to read codes with precision.
Impact of Environmental Factors on Barcode Readability
Environmental variables affect vehicle DPM code legibility in various ways. Different lighting, dust, and oil affect barcode reading accuracy and performance. Dust and oil can obscure codes, making standard scanning methods ineffective. Fluctuating light in production environments can also complicate matters.
Traditional scanners, which function in controlled environments, struggle to maintain accuracy in such challenging situations.
New Scanning Techniques for Automotive DPM Codes
Given the inherent difficulties of conventional scanning techniques in the automotive sector, a new approach is needed. Dynamic scanning technologies are specifically engineered to meet the distinct requirements of DPM codes within the manufacturing setting. These cutting-edge solutions, which include innovative applications and 2D imaging scanners, represents a paradigm shift toward increased productivity and accuracy for automotive manufacturing.
Low-Quality Camera for Barcode Image Capture
The performance of barcode scanner cameras plays a pivotal role in accurately scanning Direct Part Marking (DPM) codes within the automotive industry. These codes are intricately inscribed on tightly spaced components. Poor camera quality may lead to suboptimal code scanning, causing distorted image capture and erroneous information decoding or error messages.
Moreover, DPM codes on numerous automotive parts are positioned in remote areas within vehicles where adequate lighting is inaccessible. Consequently, subpar camera quality faces challenges in capturing clear images under low-light conditions.
The Rise of Scanning Technologies in the Automotive Industry
Modern barcode scanning technologies, such as 2D Imaging Scanners, have revolutionized DPM code scanning in the automotive industry. These scanners provide greater accuracy and reliability for enhanced data capture, irrespective of the challenging environments.
Applications of 2D imaging scanners in reading DPM codes
2D image scanners are known for reading DPM codes with high accuracy, capturing even the most complex images. These scanners can easily outperform conventional scanners to improve efficiency within the automotive setting.
Benefits of Using Advanced Scanning Systems in Automotive Manufacturing
The introduction of intelligent scanning systems marks the start of a major transformation in the automotive industry. Benefits include improved efficiency and quality control, leading to higher accuracy, faster processing times, and better traceability.
-
Increased Accuracy: Modern scanning systems ensure that data is captured correctly, which cuts down on errors in tracking and recognition.
-
Better Traceability: Improved traceability enables precise tracking, enhancing compliance and quality control.
-
Faster Processing Times: Modern scanning solutions enable expedited data processing, which optimizes production processes and mitigates operational constraints.
Implementing DPM Code Scanning in Your Automotive Facility
When striving for accuracy and productivity, it is critical to prioritize the selection of an appropriate scanning solution. This section explores significant factors to be taken into account, including system integration, DPM code categories, and environmental influences.
Considerations for Selecting the Right Scanning Solution
When considering the scanning solution for an automotive facility, it is important to consider environmental conditions, integration with pre-existing systems, and the specific DPM codes being used.
- Barcode Compatibility: Check if the barcode scanning solution is compatible with specialized DPM codes used in automotive operations, such as Data Matrix or QR codes.
- Integration Compatibility: Consider options that can easily integrate with preexisting infrastructure, such as ERP and MES, to ensure a unified process.
- Environmental Resistance: Check that the scanning solution can endure tough conditions such as oil, dust and variable lighting.
- Scanning Efficiency: Assess efficiency and speed to enhance manufacturing procedures and eliminate congestion.
- Durability: Select a reliable and resilient solution ideal for the rigorous automotive manufacturing environment.
Getting Started with Dynamsoft Barcode Reader SDK
Dynamsoft Barcode Reader SDK (DBR) is a reliable solution for DPM code scanning. It provides state-of-the-art functionalities tailored to address the unique requirements of the automotive sector. Organizations seek to optimize their processes in the dynamic realm of automotive manufacturing. To achieve this, the DBR provides a streamlined solution that enables seamless integration and unlocks the possibility of improved traceability and operational excellence in DPM applications.